Calculating product cost is important for factory management to understand the expenses involved in creating a specific product. As opposed to the total production cost, which reveals the overall costs of the entire production line, product cost looks at one product at a time and enables management to compare and contrast the expenses created by different products.
There are three elements involved in calculating product cost:
- Direct material – all of the measurable raw materials that are used in creating the finished product.
- Direct labor – the salaries and benefits paid to the workers directly involved in the production process during the time that they are working on the specific product.
- Factory overheads – indirect expenses that aren’t easily applied to the direct material or direct labor categories. This includes costs like salaries of managers and administrative staff, electric and utility bills, depreciation of equipment, etc.
The formula used to calculate total product cost is:
Total product cost = direct materials + direct labor + factory overheads
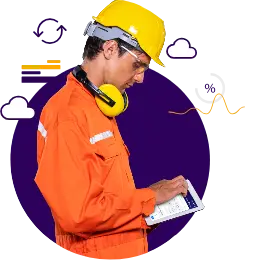