How to Adjust Your Approach to Manufacturing KPIs for 2023
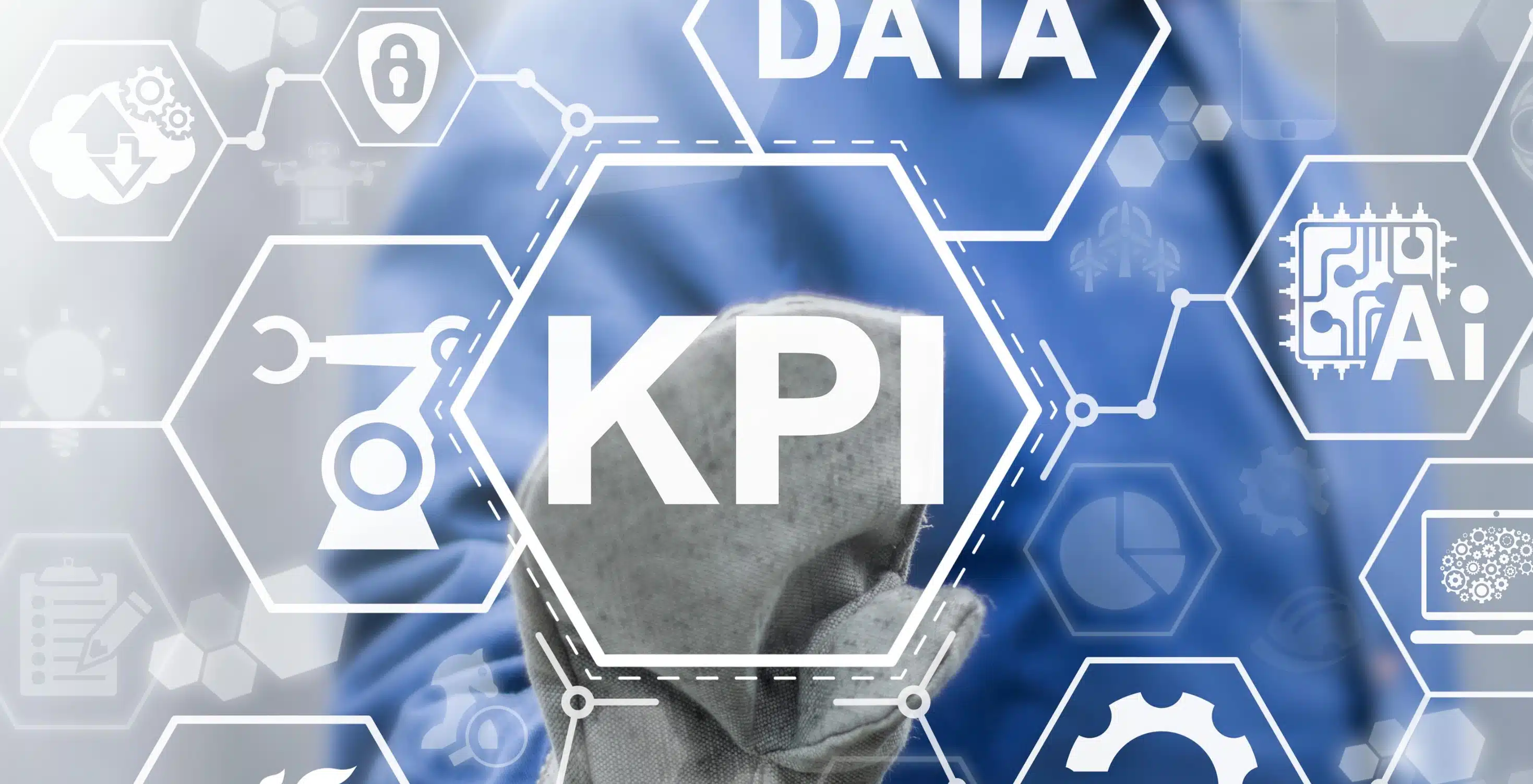
As the new year approaches, many manufacturers are reviewing their management practices and workflows to find opportunities for improvement. How you define, monitor, and manage your KPIs on the shop floor is one area where you could improve in 2023.
Changing how you understand and use KPIs can benefit productivity and your bottom line, so making these adjustments should be a top priority for any manufacturer.
Aligning KPIs With Your Sustainability Policy
With new commitments toward sustainability from governments worldwide, many manufacturers are seeing increased scrutiny and regulation over their emissions and waste. Your sustainability policy has likely changed over the past year, and your KPIs must align with it.
The KPIs you’ll need to track to ensure internal policy and regulatory compliance will vary by industry. In plastics, recycled material content is becoming more critical to monitor for all work orders. You’ll need to monitor accurate material consumption KPIs to ensure and demonstrate compliance with new rules.
In many industries, scope 2 and 3 emissions now factor into sustainability policies. To develop rigorous emissions accounting, you need KPIs that accurately reflect the impact of upstream and downstream emissions. This can have regulatory implications and affect the perception that consumers and industry partners have of your organization.
Taking a Closer Look at Energy Consumption
Energy consumption KPIs are often overlooked compared to material consumption, quality, and other areas of focus on the shop floor. Your organization could be missing out on opportunities to reduce waste and optimize energy consumption due to a lack of high-resolution energy consumption KPIs.
In modern manufacturing, there’s no reason why energy consumption KPIs can’t focus on individual machines and processes. While many utilities have traditionally been monitored in terms of consumption for the entire facility, advancements in meter technology, IoT devices, and connectivity make monitoring energy consumption KPIs for most machines physically and economically viable.
The same principle is valid for the time frame that energy consumption KPIs target. Averaged consumption over any considerable period of time provides little insight into the impact of spikes and other events. Real-time energy consumption data makes it possible to link energy consumption KPIs to events on the shop floor and to identify and implement potential improvements.
Linking Your KPIs to Production
Manufacturers have access to a wide range of production data that allows them to define and monitor many different types of KPIs. However, manufacturers must ensure that their KPIs have real connections to efficiency, productivity, and costs. KPIs without that essential context can lead to incorrect conclusions and opportunities being overlooked.
Most KPIs can also be evaluated in terms of production. Raw material consumption provides a direct example. Raw material consumption simply in terms of tons or tons per hour doesn’t provide any context or insight. Instead, the KPIs to monitor are tons of consumption per weight or the number of units of production completed. Monitoring this KPI gives clear insight into when too much material is being used and allows manufacturers to set benchmarks and goals.
Other KPIs can be similarly linked to production. Energy consumption, in particular, can provide greater insight when evaluated in terms of production. Monitoring kWh per kg or unit of production can highlight process disruptions, identify waste sources such as idling machinery, and provide insight into opportunities for optimization.
Incorporating KPIs Into Your Daily Operations
KPIs aren’t something that should only come up in quarterly reports and reviews. Instead, they can be a valuable part of your daily operations. Reviewing KPIs after the fact can provide benefits and guide overall strategy, but using real-time KPI monitoring can improve efficiency and productivity on the shop floor during production.
With the right solution in place, real-time KPIs can serve as triggers for alerts and automated workflows. Automated monitoring can reduce latency between events and their resolution by triggering these alerts whenever KPIs leave set thresholds. Access to current KPIs for a work order or shift also lets production teams and other stakeholders orient themselves and do their jobs better.
Update KPIs for New Goals and Targets
KPI management is an ongoing task that requires frequent input as internal and external factors affect your organization’s goals and targets. The end of the year is an excellent time to review KPI targets and thresholds to determine if they’re still in line with the organization’s overall strategy.
If your shop floor has changed over the last year, your KPI targets should change with it. New equipment, better workflows, and other improvements could have shifted your shop floor’s reasonable expectation for productivity. If KPI targets and thresholds don’t reflect these improvements with more ambitious targets, then you aren’t making effective use of the monitoring and tracking you have in place.
Building a Better Understanding of Downtime
Planned and unplanned downtime both have a significant impact on productivity. Machine availability and performance are both common KPIs that can help track and understand downtime, but it’s vital to collect enough information on stop events to make continuous improvements to processes.
KPIs concerned with maintenance can help reduce downtime. With the right solution, you can track stop events on your shop floor and compare them with other KPIs in quality and other areas to develop a predictive maintenance plan. This lets you anticipate the need for planned maintenance based on KPIs before unplanned stops can impact productivity.
Focusing on Setup Time
Setup time is another area that impacts productivity. It is often overlooked by manufacturers, given its brevity compared to the overall time commitment for work orders. However, it’s typically one of the most effective areas to target to improve productivity.
Tracking setup time KPIs across time can allow manufacturers to develop benchmarks and identify opportunities for improvement. With accurate data on how long setup takes for specific machines, products, and other factors, you can understand how to improve efficiency and reduce waste at this critical step.
Make KPIs More Accessible for Stakeholders
If your organization keeps KPIs relegated to boardrooms instead of using them on the shop floor, you’re overlooking significant opportunities to improve production. A platform that makes KPIs easily accessible to stakeholders can increase team engagement and encourage individual stakeholders to feel a more direct responsibility for reaching targets and goals.
Providing access to KPIs and other production data with fewer barriers between individual roles and departments also improves collaboration and lets your organization benefit from the synergy your teams can achieve. KPIs spread throughout multiple systems or spreadsheets or restricted to specific departments are less likely to be put to good use. Improving access throughout the organization lets manufacturers leverage the full value of KPI monitoring and tracking.
Changing Your Approach to KPIs With Matics
Changing how you define, monitor, and manage KPIs in the coming year could provide your organization with a wide range of benefits. However, you need the right tools to implement those changes. Matics Real-time Operational Intelligence (RtOI) is a comprehensive solution that can do just that.
Matics RtOI aggregates and analyzes data from your shop floor and across your organization, providing insights through an intuitive platform with built-in communications for your team. You can monitor and track KPIs in real-time and over periods of time, setting thresholds that trigger automated alerts and workflows. Define custom KPIs that best suit your process needs and customize dashboards for different roles and stakeholders to ensure maximum impact across your organization.
Our team can provide you with a demo highlighting our platform’s unique features and demonstrating how it can take your KPI management to the next level.