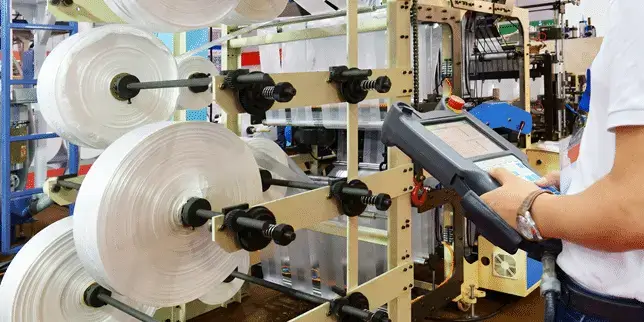
The manufacturing industry has long debated the difference between the terms MOM and MES. Some people think the two are essentially the same and can be used interchangeably; others feel there is little difference between them and want to collapse the two into a single term. Yet another crowd believes that one represents an evolution of the other and should supersede the older version.
What is the real difference between MOM and MES, and why does it matter? Beyond achieving clarity on a long-debated topic, establishing precise definitions is critical for manufacturers looking to invest in manufacturing operations management software. Differentiating between the two labels helps provide a better understanding of what a particular manufacturing software solution is and what it can do.
With the ongoing development of Industry 4.0, the discourse around these terms has become even more complicated. Many solutions are transitioning away from these classic labels altogether, including Matics Real-time Operational Intelligence (RtOI). RtOI fulfills many of the roles of both of these systems, along with entirely new features. Manufacturers need to understand exactly what a solution can do for them before making their choice.
MOM vs. MES
MOM stands for Manufacturing Operations Management. In the strictest sense, MOM refers to the third layer of the ISA-95, a set of standards designed by the International Society of Automation used to make accurate comparisons of production levels at different locations. This new set of standards was introduced around 2005 to more accurately describe what was possible with emerging digital solutions.
The ISA MOM layer includes a range of systems vital to production management, including quality control, materials management, and more. It also encompasses logistical concerns like platform security and staff scheduling.
MES, on the other hand, stands for Manufacturing Execution System. In the framework of the ISA-95, MES is considered a subset of MOM, referring to one of the many inputs that are required to run a well-managed automated facility.
This term is significantly older than MOM, originating in the mid-1990s. MES is less commonly used to refer to business processes, generally being applied only to the tools that drive them. While you will still see instances in which these tools are described as MOM software, the MES term is considered more correct in this context.
The major differentiator between the two is their scope. MES is directly tied to events on the factory floor. MES software can help manufacturers meet larger production management goals, but its primary purpose is to monitor, manage, and optimize the day-to-day processes inside the facility using data. MOM, on the other hand, is primarily concerned with business operations as a whole. It is linked to larger business concerns like supply chain efficiency and automation, working toward greater efficiency on a much longer time scale than MES generally does.
The Evolution of Manufacturing Operations Management Terms
In spite of the current distinctions made between MOM and MES, it is important to understand that the language used to describe manufacturing business processes has a long history of continual change.
Over the years, many terms have been used to describe similar tools and concepts, including PDM (Product Data Management), ERP (Enterprise Resource Planning), and CIM (Computer Integrated Manufacturing). Each was once considered the standard term for this type of data-driven production planning in manufacturing, and some of them are still in use today.
These other terms likely produced less confusion because they used different letters in their acronyms, making them more clearly distinct from one another. MES and MOM, unfortunately, share the same first letter and total acronym length; at a glance, they look nearly identical. This makes it easy to confuse them or to mistakenly use them interchangeably. Further complicating the issue is the fact that MOM is often used over MES for marketing purposes by software companies who wish to position their solution as the latest and greatest thing.
It should be noted that the evolution process described here is ongoing and that preferred terms for certain concepts will inevitably continue to shift over time. As manufacturing operations management software solutions are built with more and more MOM functionality, they may be referred to as MOM software by a greater portion of the industry. Some of the more robust versions on the market today include enough advanced business-related features that an argument could be made for the use of either term.
MES Explained
Distinguishing between MOM and MES is vital for businesses hoping to implement the latest manufacturing operations management software inside their facilities.
The term MES was introduced specifically to serve as a successor to CIM, a term that was most common during the mid-1980s. The idea behind the shift in language was to reinforce a vision of computerized manufacturing that treated each part of the manufacturing process as a distinct sphere with its own strengths, weaknesses, and requirements.
In this model, each process can be examined, analyzed, and improved on an individual basis. The model does recognize that each of these processes integrates with one another to form a cohesive whole, but this is not its primary focus. Rather, it emphasizes tracking and optimizing smaller-scale metrics to produce small but targeted improvements. In combination, these small changes often add up to more significant efficiency gains across the board.
This type of granular analysis was very difficult to accomplish with the software available at the time the CIM term was in use. When technology evolved sufficiently to expand access to individual process analytics, the MES term became more widespread as well. Now that technology has progressed even further, real-time analytics are becoming increasingly commonplace.
These developments have further improved manufacturers’ ability to manage their operations according to the MES model. As a result, this type of manufacturing operation system has become more powerful and more applicable than ever before. Manufacturers must not mistake it for an inferior tool simply because it uses terminology that some consider outdated; the term MES actually underscores its main strength.
What MES Implementation Can Do
After so much discussion of the specifics of manufacturing software terminology, it is important to return to the reasons why the distinction matters in the first place. What can MES management solutions do for a manufacturing business, and why should manufacturers install them in their factories?
MES software can play a significant role in a manufacturer’s present and future success. A modern cloud-based MES solution provides an extensively detailed picture of the current status of the factory floor, and it continuously updates that picture as production conditions change over the course of time. This works to keep key stakeholders apprised of every major and minor event taking place inside the facility, whether it happened last year, last week, or 30 seconds ago. It can even be used to predict certain negative events before they happen based on historical data patterns.
Among other things, MES software can be used to:
- Collect data from machines, sensors, and IoT devices to accurately track all aspects of production on a real-time basis.
- Implement proactive machine maintenance, staffing, and materials management protocols to maximize machine availability.
- Alert workers to emergency issues on the factory floor, such as a sudden work stoppage or quality control issue.
- Accurately forecast short- and long-term future production to better meet purchaser demand.
- Facilitate communication between workers, managers, technicians, and other relevant parties.
- Enable in-depth analysis with stored historical data and easily digestible visual displays.
- Guide efforts to streamline production with factual data to support decision-making.
The impact of MES implementation is felt immediately, and its influence quickly compounds into significant efficiency improvements that can be carried forward into future production rounds. It creates an environment of complete transparency on the factory floor, making it possible to address urgent issues immediately as they arise. The sooner these problems are corrected, the less they are able to disrupt production and incur losses for the facility.
If the knowledge it provides is used to implement permanent changes, MES software can eliminate much of the time and material waste that occurs in a factory setting.
Changing the way people work in factories
Request a DemoIndustry 4.0 Solutions Take These Capabilities Even Further
Today, Industry 4.0 solutions such as Matics RtOI are providing even greater capabilities for manufacturers. Like a top-notch MES, RtOI aggregates data from machines, sensors, and IoT devices. However, RtOI also draws valuable information from other sources and systems. RtOI can work with existing MES and MOM systems to provide a truly holistic approach to running your factory floor.
The real-time monitoring of this production data can be finely tuned to an individual manufacturer’s unique needs with custom KPIs and event triggers. Predictive capabilities even make it possible to take action before a process loses control based on historical production data.
The scope of action that manufacturers can take with this real-time data and analysis has also increased. RtOI implements advanced work management tools that go far beyond simple alerts. Entire workflows can be put into action in response to events, involving multiple stakeholders and ensuring that each one has the information and context needed to act immediately.
While distinct MES and MOM systems still exist, we’re already starting to see another shift in the way the industry categorizes these systems. As Industry 4.0 solutions continue to advance, holistic systems like Matics RtOI are quickly becoming necessary for manufacturers to remain competitive.
MES Implementation for Manufacturing Success
The rivalry between MOM and MES within the manufacturing industry is not merely a semantic scuffle. Manufacturers should not be wary of software solutions that embrace MES terminology in their marketing, but instead, recognize the value and inherent innovation of the MES management approach.
If you’d like to explore the potential of MES management in your manufacturing plant, Matics is the tool for you. Our cloud-based MES makes manufacturing operations management easy, providing detailed information on everything happening on your factory floor and paving the way for permanent efficiency gains inside your facility.
With Matics RtOI, you can achieve an unparalleled level of visibility and control over your factory floor, making it possible to reduce waste, optimize processes, and continuously improve your manufacturing operation.
Contact us today and let us tell you more about how our solution works and how it can assist you in your efforts to optimize processes in your manufacturing plant.