More Companies Are Turning to Green Manufacturing – How Are They Doing It?
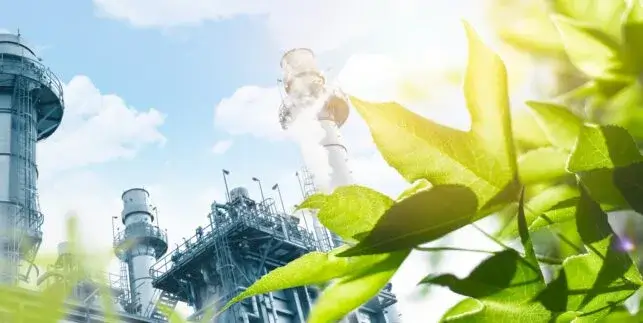
Green manufacturing has quickly become one of the most pervasive topics throughout the industry. Manufacturers around the world are rapidly adopting eco-friendly manufacturing. They’re doing so by implementing a variety of new methods and transforming their operations into green factories capable of meeting modern sustainability standards. Your operations may already be falling behind if you haven’t embraced the importance of going green.
What Is Green Manufacturing?
Green manufacturing is one of many terms that has become more relevant in recent years. There is significant overlap with sustainable manufacturing processes, but also some key differences. What is sustainability in manufacturing? It’s an approach that takes into account all aspects of ESG impact, including environmental, social, and governance. Green manufacturing is more strictly focused on the environment.
Green manufacturing definitions focus on various impacts, including air and water emissions, waste, natural resource use, and energy. A green manufacturing company prioritizes these areas, whether out of their corporate values, to meet regulations, or to improve public image. They implement measures to measure and control their impact in the hopes of ensuring a better environment for the future.
Why Is Green Manufacturing Important?
There are many environmental crises that are coming to a head in the near future, with some showing significant adverse effects already today. Climate change is the most widely discussed example, with the impact of CO2 and other greenhouse gas emissions now under close scrutiny by governments around the world. Manufacturers must contend with emissions involved in energy production, transportation, and related to the production of raw materials.
Climate change is just one area that a green manufacturing company must address. There is also the impact of material waste in terms of both waste to landfill and waste that makes its way into the environment. Plastic pollution is a prime example, with the growth of both marine plastic pollution and microplastics in every environment highlighting the need to reduce waste.
Implementing solutions to these and other challenges is essential to secure a clean and healthy environment for future generations. The modern green factory seeks to do just that.
Why Are So Many Manufacturers Moving Toward Green Production?
Sustainable manufacturing companies have been developing rapidly over the past decades and have continued to accelerate. Today, there are many factors driving all types of manufacturing operations to improve their environmental impact.
First and foremost is government regulation. Countries around the world have made environmental commitments, such as the goal of reaching net zero CO2 emissions by 2050. These nations, in turn, apply regulations to their industries in order to move toward those goals. Manufacturers may face considerable fines for excess pollutant emissions, energy use, or material waste. There are also incentives in many cases for operations to adopt green production methods and technologies.
Manufacturers face similar pressure from the general public. Environmental sustainability is among the most valued criteria among consumers. Organizations must maintain the image of green manufacturing if they wish to compete in the modern landscape. While there is still debate in many cases over just what are green products, there is considerable pressure for companies to at least attempt sustainability.
Many sustainable manufacturing practices are also implemented due to the genuine values of the company and its leadership. The case for green manufacturing is incredibly strong, and individuals at all levels are looking for ways companies can go green.
How Are Green Manufacturers Achieving Sustainability Today?
Making a commitment to green manufacturing is easy. However, making actual changes can be a challenge. These are some of the green manufacturing examples that companies are already putting in place today to meet their environmental sustainability goals.
Reducing Packaging
Packaging has been at the center of the debate over material waste for decades. Over the past decades, plastics have quickly become the standard for packaging in many types of consumer goods. Unfortunately, much of that packaging has worked its way into the environment.
One way that manufacturers are going green is by reducing overall packaging in their products. Traditional packaging methods could feature excess material and padding. They also often included unnecessary individual packaging within larger containers. Changing the design of packaging helps manufacturers cut down on that waste.
This provides a variety of benefits for manufacturers. They improve their public perception. In many jurisdictions, they are required to do so by law or face increased taxes or other penalties. There is also the direct cost savings associated with using less material. Overall, reduced packaging is one of the most straightforward and effective steps that green manufacturers can take.
Reducing Waste on the Factory Floor
Packaging waste and the final disposal of a product are both serious issues to address in the design of any product. However, there is also waste that takes place behind closed doors. On the factor floor, inefficient processes and quality issues can lead to the substantial waste of both materials and energy.
A process with high reject rates is one example. Manufacturers might produce many more products than are needed to make up for the amount they need to scrap. Even in processes where defective units have their materials recycled, there is still a waste of energy.
Tightening quality and adapting processes to minimize waste, whether due to rejects or trim in various steps, is another essential step in realizing green manufacturing. Increased regulation and the introduction of waste credits in some countries are pushing manufacturers to reduce waste on the factory floor.
Transitioning to Alternative Materials
For many products, the material used in the product itself presents an environmental concern. This is seen clearly in plastics manufacturing, where many products find their way to the environment and can take centuries to break down. While less prominent, other materials can also pose serious issues.
Some manufacturers are responding by changing the materials they use in their products. This could mean using a type of plastic that is more easily recycled, biodegradable, or made from plant fibers. Other examples substitute plastics for cardboard or paper.
Making these changes requires significant design and testing to ensure product quality. In some cases, it simply isn’t feasible. In others, it would mean exorbitant investment in new process equipment. Despite these challenges, many manufacturers are still making the change to improve public perception and meet new regulations.
Choosing Renewable Energy
Energy-intensive processes that rely on energy from fossil fuels such as natural gas and oil produce significant greenhouse gas emissions. Even where manufacturing operations rely on electricity, most countries still have grids supplied by a majority of fossil fuel sources. Transitioning to renewable energy is one way that manufacturers can reduce their emissions impact.
In some processes, the use of replacement fuels is a promising option. Bio-diesel, ethanol, hydrogen, and other alternatives to fossil fuels serve to eliminate emissions or derive them from resources used in the natural carbon cycle.
In other cases, green factories are finding ways to generate electricity on-site from renewable sources. Many facilities are making use of ample roof space or even building canopies over their parking lots for solar panels. Geothermal HVAC, improved control systems, and other advancements are further enhancing their energy efficiency.
Embracing Cradle-to-Cradle Design
Cradle-to-cradle design is a concept in green manufacturing focused on creating sustainable production ecosystems. The idea is similar to that of a circular economy, where materials are recycled indefinitely, such as in many metal applications. However, it also encompasses a broader scope where material routes aren’t necessarily circular but are built in more complex ways as well.
In practical application, this means designing products in a way that they have a planned end-of-life use. This may not necessarily mean recycling used products back into the same raw materials but could include processing to any number of potential applications.
This is already seen in many industries that handle materials that degrade over time. Many types of plastics are downcycled, as the recycled feedstock has properties that make it unsuitable for the same applications as fresh feedstock. For example, HDPE plastic bottles are often recycled into rougher products with solid coloration, such as tables and benches.
Informing Consumers
Another key element of green manufacturing is making it easier for consumers to get involved. Sustainable manufacturing practices have quickly become key selling points for many types of consumer goods. Manufacturers are making changes, and they want consumers to know about it.
Green labeling has become much more common. However, there has also been a rise in cases of supposed green-washing. Some companies make green claims that don’t carry the weight they imply. While outright fabrications are rare, manufacturers don’t always present their sustainability efforts honestly.
True green manufacturers go out of their way to educate consumers on the specific issues their production methods are addressing. Whether that’s greenhouse gas emissions, waste reduction, or renewable energy, they focus marketing and consumer packaging on communicating the impact that they have.
What Technologies Are Helping Manufacturers Go Green, Now and in the Future?
With every green initiative put in place comes the challenge of implementing it on the factory floor. There are many logistical and practical elements to realizing any change. In some cases, they are only made possible by new technologies. Green manufacturing tech is advancing rapidly, with these sustainable manufacturing examples highlighting how tech is making a difference today.
Material Advancements
Many of the most promising advancements in green manufacturing have come in the form of new materials. The simple fact of the matter is that many of the most polluting materials are only used because there aren’t any green alternatives.
Bio-polymers, bio-composites, cellulose-based materials, nanomaterials, and a variety of other materials are providing substitutes for non-biodegradable plastics and other materials that work their way into the environment.
Real-time Monitoring
When it comes to reducing waste on the factory floor and implementing new green initiatives, few technologies are more valuable than real-time monitoring. While many facilities have had to rely on occasional checks or batch data, today’s new systems allow for real-time production data.
These solutions don’t simply collect data but provide analysis and insights in real-time as well. Manufacturers can monitor material and energy waste, product quality, and a range of other criteria that go into green production.
New Sensor Tech
Handling the wealth of production data in a way that generates the most benefit is key to green production. However, unlocking new sources of data is also a tremendous benefit. New sensor technologies are enabling waste reduction and improved efficiency on factory floors.
Improved visual sensors are one example that is already seeing widespread use, improving quality control to tighten tolerance and reduce waste. Other examples include auditory sensors to identify potential issues throughout processes. These new types of data are powered by AI analysis that draws unique insights to improve operations and maintenance.
Enhanced Connectivity
The lack of connectivity in traditional manufacturing has posed a significant barrier to many green initiatives. Today, the Internet of Things and other improvements in machine connectivity allow for a more holistic production environment. Management and production teams can enjoy improved visibility and control, letting them implement changes more effectively.
This also applies to connectivity throughout the organization, not just to machines. Providing access to production data, scheduling, and other key features through a cloud solution lets stakeholders monitor and react to changes in the production environment from anywhere. Improved collaboration and reaction times help reduce waste and improve efficiency for greener production.
Changing the way people work in factories
Request a DemoIs Your Factory Floor Ready to Embrace Green Manufacturing?
Green manufacturing is quickly becoming the standard, not the exception. As regulations become stricter and public perception continues to turn in favor of green manufacturing practices, your operations can’t afford to miss out.
Realizing green manufacturing on your factory floor requires visibility and control. You need a way to put initiatives in place and metrics to understand their progress and impact. Matics Real-time Operational Intelligence lets you do just that. Achieve real-time visibility and take advantage of unique insights into your operations. Manage changed recipes, monitor green initiatives, and streamline scheduling and setup for new processes. Reach out for more on how Matics can help you go green today.