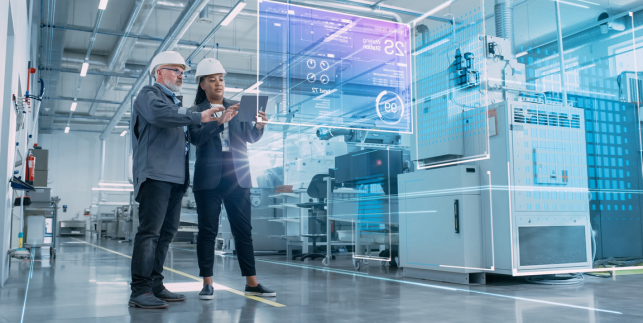
The US manufacturing sector faces a wide range of challenges, from ongoing supply chain shortages to offshore competition. Today, one of the most significant hurdles for manufacturers to overcome is the shortage of labor. Advanced manufacturing operations require skilled individuals at every level, and many struggle to fill and retain those positions.
Manufacturers are now turning to a variety of strategies to overcome these challenges. Recent legislation, both in the US and abroad, has resulted in more investment in education and other programs to close the skills gap, but the results of these efforts are still years away. These strategies let manufacturers take action today to build stronger and more resilient teams.
Increasing Wages in a Competitive Market
With an ongoing labor shortage affecting businesses of all kinds, much of the public debate over the issue has been focused on wages. The manufacturing sector has always provided attractive wages for workers at all levels of education and experience. Still, many manufacturers are now seeing increased pressure to increase their offers to compete in the labor market.
Data from the US Department of Labor shows a clear increase in hourly compensation in the manufacturing sector. Hourly compensation has increased by 2.7% over the last year, with the fourth quarter of 2022 trending for a 3.2% increase. These increases come even with a 1.5% decrease in labor productivity over the last year, pushing unit labor costs even higher.
Labor is second only to raw materials in terms of costs for almost all manufacturers. Increasing wages present a significant hurdle to overcome if manufacturers can’t effectively and efficiently use their human resources.
The growing use of sign-on bonuses in many of the most critical and competitive positions has introduced further labor concerns. This type of competition encourages churn within the industry, preventing organizations from developing employees to reach their full potential over time.
Creating a Hybrid Work Culture
With the onset of the COVID-19 pandemic, many sectors rapidly transitioned to remote work and hybrid work arrangements. Many faced considerable challenges, given the scramble to implement the technology and solutions needed to support remote work. The landscape has since become more stabilized, and working remotely is one of the most attractive features of any position.
A survey by McKinsey shows that 35% of US employees across all industries have the option of working remotely on a full-time basis. A further 23% have the opportunity for part-time or occasional remote work. However, implementing a hybrid work culture in manufacturing operations presents various challenges.
Even the most heavily automated manufacturing operations require on-site personnel. There are key aspects of what operators, technicians, and other roles provide that require physical interaction with machines and products. With many remote work opportunities available in other sectors, manufacturing is struggling to attract new applicants.
However, manufacturers have many opportunities to enable hybrid work culture and even fully remote work for certain positions. Industry 4.0 technology makes improved remote visibility and control possible. With a secure cloud solution, real-time production data can be accessed by authorized employees from anywhere.
The manufacturing sector still requires boots on the ground for many roles and will continue to do so for the foreseeable future. However, using technology to implement hybrid work culture where possible lets manufacturers make specific roles more competitive, tackling one aspect of the labor shortage.
Upskilling Existing Team Members
It’s better to retain an employee than hire a new one. Your workforce is made up of skilled employees who have come to know your operational and business processes, making them more efficient and effective. While attracting new employees is an ongoing challenge, manufacturers shouldn’t overlook the value of their current workforce.
Upskilling is one of the best ways that manufacturers can invest in their existing workforce to see real improvements in their operations. As manufacturers continue to adopt new processes and technologies, providing their experienced team members with the necessary training and education ensures that they continue to deliver exceptional productivity.
This can take the form of both overall training for roles throughout your workforce or the development of individuals to better leverage their unique skillset. Upskilling can mean filling gaps higher in your organization from within and providing the training and education that experienced employees need to take on new roles.
Relying on employees who already understand key aspects of your operations instead of hiring from outside can reduce the costs and time associated with onboarding. It also ensures that your team has insight into your operations from multiple perspectives, enabling them to provide even greater value.
Upskilling also serves as a vital part of retaining your workforce. Employees highly value this kind of development. A Gallup study revealed that 48% of US workers say they would switch jobs if offered the right skills training opportunities.
Reducing Manual Tasks Through Automation
It’s clear that much of the focus of both manufacturers and legislators is rightfully placed on developing a skilled workforce. However, automation also plays a vital role in alleviating the labor shortage. Manufacturing already relies heavily on many different levels of automation, and Industry 4.0 technology is now providing even more opportunities.
Manufacturing operations have long used various types of automation to reduce the need for manual tasks and monitoring. The rise of what most people would consider modern automation arose in the late 1960s with the first programmable logic controllers (PLCs), a technology still in wide use today.
However, Industry 4.0 technology is making a much broader range of automation possible. Instead of controlling individual parameters, centralized solutions can now control entire factory floors. IoT devices enable data collection from and control of nearly any machine or system, even legacy hardware not designed with automation in mind.
Implementing automation in the right way can reduce overall labor requirements. New technologies now allow for different kinds of control, monitoring, and inspection to be handled without direct human intervention. While there is still a need for skilled operators and technicians, the overall labor requirement is greatly reduced.
Empowering Teams With Advanced Manufacturing Tools
Automation is one of the core aspects of how manufacturers are addressing the labor shortage, but a new trend has emerged in advanced manufacturing. Instead of replacing or reducing them with machines, the focus is now set on empowering and augmenting human resources with advanced manufacturing tools.
Industry 4.0 solutions that offer improved visibility and transparency are one example. The right solution can consolidate important process data in real-time, analyze it, and provide key insights for production teams and management. They can then focus their efforts on decision-making and execution rather than the relatively low-value task of manual data aggregation.
The right tools also serve to enable skilled employees to navigate workflows more accurately and effectively. The ability to schedule and control operations through a single platform with clear insight into the impact of any changes facilitates planning and decision-making at every level.
Leverage Industry 4.0 Technology for Your Workforce
Matics Real-time Operational Intelligence (RtOI) provides tools manufacturers need to empower their workforce. Eliminate time spent on manual data collection, monitoring, and analysis, and take advantage of work management tools that let your team do their jobs better. See how our solution can deliver productivity, efficiency, and a better experience for your team by scheduling a demo today.