The Industry 4.0 Maturity Index: 6 Levels Toward Digital Transformation
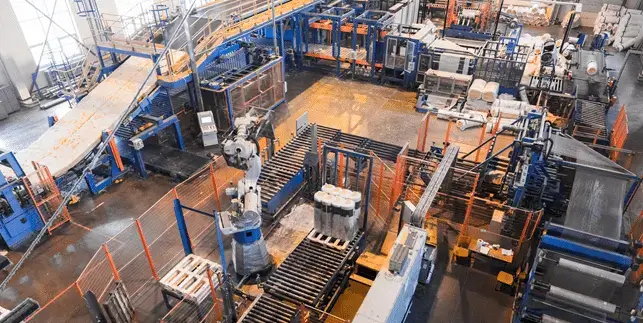
Each year, as technology advances, the manufacturing industry gains new and exciting opportunities. Industry 4.0 is perhaps the most promising among current emerging trends. This six-stage process of the industry 4.0 maturity index outlines the journey each manufacturer takes toward digital maturity, from employing nascent digital solutions to automatically leveraging the predictive powers of a fully connected network of machines.
Factories can employ digital manufacturing to greatly increase their productive potential, but not all facilities are equally ready to take advantage of this technology. Those who can reach the later stages of digital maturity now have the chance to surpass their peers and capture a greater share of their industry’s customer base.
The Six Stages of the Industry 4.0 Maturity Index
The Industry 4.0 maturity model is comprised of six sequential stages that manufacturers gradually move through as they upgrade their digital capabilities.
- Stage 1: Computerization
At this stage, companies are using digital solutions like CNC machining. However, these solutions are all operating in isolation. They are not connected to each other, and there is no way of coordinating a combined effort between them without significant manual input. Any production data they collect is also individualized, siloed, and only available after production has already concluded.
- Stage 2: Connectivity
Companies advance to this stage when their digital solutions are connected to each other in some way. It was possible for manufacturers to reach this stage as far back as the early 2000s by connecting their machines to the internet. This stage allows for some communication between machines, but it is usually slow and ineffective. The connections lack the agility to keep up with production events as they happen, leaving a gap between the data and the observable reality on the factory floor.
- Stage 3: Visibility
By the third stage of this process, manufacturers have overcome this bottleneck and now have access to a ‘digital twin’ of their factory-made with comprehensive real-time data. This data is detailed enough to let observers know exactly what is going on at the factory at any given time, but it may lack the organization necessary to make this possible. At this point, the presence of the data itself is the only qualifying factor.
- Stage 4: Transparency
At this stage, digital development shifts from increasing technical ability to leveraging analytics. To make it to this point, manufacturers must learn to interpret and understand the data they have collected. Most shop floor control software performs this type of analysis automatically, sorting and displaying relevant data in response to user inquiries.
- Stage 5: Predictive Capacity
Here, manufacturers use the real-time data at their disposal to make predictions about the future of their production capabilities. This includes insights into matters such as when work stoppages might happen, when quality control may be failing, where a facility can save on energy consumption, and more. This is another area where shop floor control software has a significant role to play.
- Stage 6: Adaptability
At this final stage, digital systems within the facility gain the ability to act independently using their analytic and predictive abilities. They can take action to adapt to changing conditions as they unfold, organizing staff and their duties to handle routine operations as well as emergencies and developing problems.
The Current State of Industry 4.0 in Manufacturing
Digitalization is a relatively new concept in the manufacturing industry, but it is gaining momentum as time goes on. Our recent survey conducted in partnership with PEX Network revealed that only 42.7% of manufacturers have fully or partially digitalized their operations as of now. A further 31.5% plan to do so in the next one to three years, but have not yet actually begun the process of implementing Industry 4.0 solutions.
It is clear that while factors such as the increasing presence of technology in our lives and the impact of the COVID-19 pandemic are driving a significant increase in facilities’ willingness to adopt digital solutions, there is still a lot of development left to occur. Many facilities are stuck in the second or third stages of the process, and a significant proportion have not even begun to approach the issue.
Embracing Digital Manufacturing Opportunities
Smart digital transformation has the ability to give factories unprecedented insight into the finer points of their day-to-day operations. With this level of insight comes great opportunity: a digital factory has the ability to optimize virtually every moment of production, minimizing loss and recouping revenue. In this environment, executive decision-making can be greatly sped up while remaining informed and grounded in observable evidence. The digital solutions simply make the necessary information more accessible.
The manufacturing industry is slowly moving toward digital maturity, but it is important to note that even those who have begun the process and have access to production data are not always using it to its fullest potential. Just 34.5% of respondents were using their data to provide real-time notifications and calls-to-action or to power advanced analytics. A mere 21.9% have full visibility on all their lines, including access to insights to help prevent recurring losses.
The underutilization of data among manufacturers gives companies who are able to harness it properly an additional competitive edge. Industry 4.0 optimization can produce dramatic increases in production that factories without similar technology cannot hope to match. Manufacturers who act quickly and choose to be early adopters in their industry will enjoy a significant boost to their capabilities that may be enough to help them take over a larger share of the market. These boosts will cease to be meaningful over time as digital maturity increases, however, so early action is critical to securing this advantage.

Changing the way people work in factories
Request a Demo
Changing the way people work in factories
Request a DemoReaching the Cutting Edge of Digital Transformation
Working with Matics makes it possible for manufacturers to push the limits of Industry 4.0 maturity. Our Real-time Operational Intelligence (RtOI) provides everything that manufacturers need to achieve a complete digital transformation and enjoy the increased efficiency and productivity that comes with it.
RtOI achieves visibility and transparency on the factory floor by aggregating and analyzing data from all sources in real time. Stakeholders throughout the organization can access the information they need to fulfill their roles effectively through a single platform with the relevant context.
Beyond that, RtOI has features that allow for automation and predictive capabilities only possible with the latest Industry 4.0 advancements. Automated production monitoring ensures that KPIs and other important metrics are kept in line, immediately notifying the appropriate individuals as soon as any event takes place on the factory floor.
Matics RtOI also features robust work management tools that take the digital transformation a step further. Manufacturers can now implement sophisticated workflows and automated responses in response to events on the factory floor. Not only can production teams respond without latency, but also with processes in place to resolve issues as quickly and completely as possible.
Bring Your Facility Into the Digital Age
Industry 4.0 is coming to manufacturing whether the industry is ready or not. The myriad benefits it offers in its later stages make it impossible for savvy manufacturers to resist. The more facilities adopt digital solutions as part of their production process, the more urgent it will be for their competitors to do the same.
At Matics, we provide advanced Industry 4.0 solutions to help factories progress through their digital development. Our software takes manufacturers from the early stages of digital development all the way to Stage 5, and it can be fully implemented by a layperson in just a few hours. Contact us today to learn more about how Matics can help you to eliminate inefficiencies, save time and resources, and ultimately boost your bottom line.