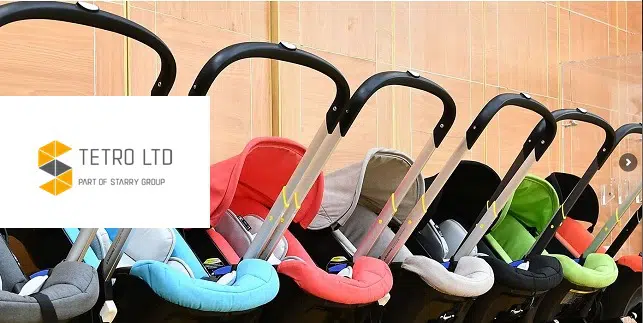
Tetro gains a real-time window into its production environment by integrating with Matics Challenges
- Controlling the production flow, tracing mistakes and optimizing performance
- Running a fully integrated knowledge-based business with systems that work seamlessly together
- Centralizing manufacturing production data into one system that can be viewed and analyzed from a single-point-of-entry
- Pinpointing in real-time which stations are compromising production and what can be done to restore and improve efficiency
- Implementing preventative maintenance and ensuring minimum downtime
- Monitoring energy consumption and optimizing material consumption per product
Highlights
- Plug & Play technology helped achieve immediate and tangible results with minimum upfront investment and no extra operational complexity
- Full visibility and real-time data collection throughout the manufacturing process in support of information-based decision making culture.
- Powerful dashboard that visualizes production data in real-time by product, machine and process
- Accumulated manufacturing data that enable SWOT process production management to maximize advantages and reduce risks.
- High ROI, tangible improvement in less than a month of operation; OEE improved by over 30% while saving on energy & Material waste, while cutting time to market by 25%
- Easy integration with dosing systems that enable precise, computerized control of material grades
- Fully integrated computerized process that prevents critical mistakes
- Monitor and compare energy consumption per product, per machine throughout the manufacturing cycle, instant notification on energy deviations.
- Compare and analyze actual manufacturing results with Tetro long-term heuristic and physical models
“Matics made it possible to collect data in real time, gain crucial predictive insights and reduce time-to-market per product by 25%. Within weeks we reached significant savings in energy consumption, master batch and materials and prevention maintenance.”
Ping Chen – Information System Manager, Tetro
TETRO Ltd., a subsidiary of the Starry Group, is an OEM manufacturer of multi-disciplinary, high-end consumer products made out of plastic, textile and metal components. Based in China, Tetro’s state-of-the-art facilities and cutting-edge technologies serve leading industry partners worldwide.
A fast-growing company, Tetro prides itself on its ability to develop and adapt innovative manufacturing methodologies, implement advanced manufacturing technologies and meet sustainability standards. Tetro’s management, in a bid to exceed market demands and consistently produce high-quality products at competitive pricing, realized it needed an accurate real-time window into its factory floors.
Data visibility became crucial in order to make information-based decisions, such as tracking and monitoring the factory’s manufacturing operations, optimizing material usage and energy consumption. The data is made transparent to Tetro’s customers who can monitor how Tetro utilizes their investments in Tools.
Tetro management wished to have better control over its manufacturing process in order to streamline the production process and identify production patterns that could help anticipate machine failures, notify management about potential production pitfalls and reduce risk of not meeting production delivery quality, cost, and timing targets.
An important cost element in the process of plastic injection and extrusion is energy consumption. Highly granular monitoring and comparing of energy consumption per each product’s manufacturing- cycle per machine will enable Tetro’s management to improve OEE and meet its sustainability targets.
The system’s planning modules help to reduce MOQ for Tetro customers which enables them to spend more on marketing and less in inventory. Tetro’s management set to create an information based decision-making culture, improved corporate transparency, and enhanced quality assurance by automatically generating real-time data reports at each stage of the production process that could provide customized per- production milestone alerts and call–to–actions.
Why Matics system?
The plastics industry faces several difficulties – increasing competition, fluctuations in material costs and growing sustainability awareness issues. Matics brings years of experience from the plastic manufacturing sector with a proven track record in streamlining plastic manufacturing processes, reducing time to market and generating significant cost savings. Matics developed specific MES modules tailored to plastic industry processes, including injection molding, extrusion dozing management and assembly.
Matics offered Tetro various solutions for machine and production monitoring, as well as real-time tracking and monitoring across the entire manufacturing process. Matics’ real time OEE reports and machine fault prediction alerts were particularly important to Tetro.
Tetro’s interest in Matics was initially triggered by Matics’ flexible and modular design making it possible for Tetro to easily configure, customize and expand the system for their own specific needs. Tetro soon recognized that by implementing the Matics system in their factories, they could run and manage a fully integrated plant with multiple systems that work seamlessly together.
With the help of Matics, Tetro could generate real-time reports on a daily or per shift basis that displayed a top-down snapshot of the entire manufacturing process. This would include machine status, material inventory, and usage, which was crucial for its daily production meetings and ongoing production assessments.
To achieve immediate results, Tetro searched for an MES system that could be rapidly deployed, configured and connected to all machines.
The Matics unique Plug-and-Play design met Tetro’s requirement for setting up an MES system within days, acquired and presented data immediately, and achieved tangible ROI within weeks of operations.
In addition, Matics team was recognized by Tetro for its high-quality, responsive support and outstanding record with previous customers in the plastics manufacturing industry.
“If I can identify whether a machine is about to breakdown or reduce its capacity and solve it, let’s say, by simply replacing a filter on time, we avoid the risk of downtime and achieve huge savings.”
Ping Chen – Information System Manager, Tetro
Matics Solution for Tetro
- Plug-and-Play modules
- Transparent and flexible
- Full visibility
- Preventative maintenance Unplanned Downtime
- Real-time monitoring of resources consumption to save costs
- Online material management & control
- Corporate sustainability policies reinforced by energy reduction and material savings
Plug-and-Play modules
The implementation of Matics became instrumental to Tetro’s operational success and long term vision of a fully visible, connected and knowledge-based factory.
Using its Plug-and-Play modules, the Matics solution was deployed across the production floor and was up-and-running within days. Following one week, Tetro was able to view production data from the factory floor and produce real time ops reports.
Transparent and flexible
Being transparent and flexible, Matics was configured to integrate with Tetro’s internal business intelligence and validation systems to meet its specific traceability and analysis requirements.
Full Visibility
Full visibility of production floor operations and material management enabled the team to monitor and track the entire plant’s day-to-day operations and resource usage in real time.
Following the integration process, Tetro’s management was given a real-time window into the plant’s production floor.
24 hour summary reports helped management and production teams review and discuss plant activity during Tetro’s daily morning meetings. Data collection made it possible for Tetro to analyze OEE information, detect patterns and trends, as well as discover where they could make adjustments and improvements. Data was documented and compared, performance was tracked, and waste was reduced.
Preventative maintenance unplanned downtime
The adjustments introduced to the preventative care process helped Tetro run smarter maintenance schedules, improve manufacturing speed, reduce unplanned downtime and prevent operator’s error. Data collected via Matics provided real time monitoring of each machine.
Additionally, an operations history log enabled the Tetro team to analyze potential production pitfalls and fix them before a breakdown occurred to achieve better and more cost effective production.
Real-time monitoring of resources consumption helps to save costs
Tetro, through the usage of Matics, was able to map and analyze power consumption data in real time. When monitoring and tracing energy consumption per product manufacturing cycle patterns per machine, Tetro was able to identify and assess machines at each station to assess what could be done to reduce its energy wastage.
Online material management & control
As material usage strongly impacts operating margins in plastic plants, it was essential for Tetro to monitor material usage at all stages of the process. With Matics’ automatic dosing control, Tetro could ensure precise and repeatable material usage. The information obtained from the Matics real-time reports at all stages of the material production process enabled Tetro to gain new insights on its production process and better control costs.