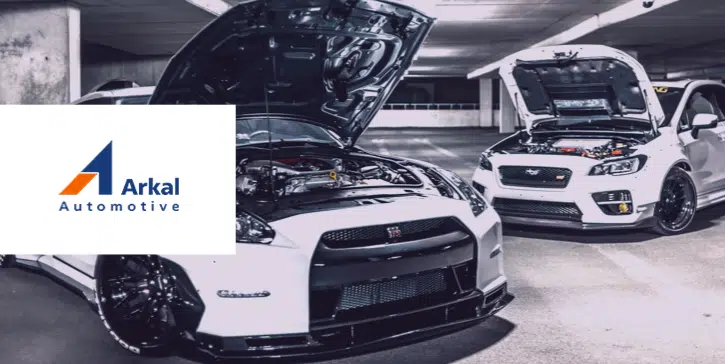
Arkal Automotive, Lightweight Plastics Design & Manufacturing
Business Needs:
- Achieve higher productivity worldwide
- Apply standard measurement worldwide, deploy automatic performance measurement tools across the business for reliability and less human user error
- Get real-time visibility on multi-site performance
- Collect data to enable data-driven decision-making
Matics Solution:
Real-time Manufacturing Analytics Platform
The Impact:
- Increased production efficiency and factory agility for Just-In-Time parts deliveries
- Created a cultural shift, improved synergy on the production floor that was strongly supported and encouraged by Matics ‒ how teams and individual personas approached their work with more transparency and collaboration
- Enabled data-driven decisions, for example, one that allowed the purchase of new machinery based on real utilization, generating enormous cost savings
- Gained complete visibility over operations in 5 countries from a single interface
- Improved machine utilization at all sites, e.g. one consistently achieves 85% OEE
About Arkal Automotive
Established in 1997, Arkal Automotive is a leading thermoplastic manufacturing supplier, serving the international automotive industry, including Tier 1 OEMs such as Daimler AG, BMW, VW, GM.
It is headquartered in Israel with factories across North America, Europe, and Asia. Their plastic parts have been revolutionizing the auto industry as they reduce car weight and minimize energy consumption.
The Challenge
The global multi-site factory confronted complex issues at local sites and across the enterprise:
- Location, Location, Location – Arkal needed to be able to meet global customer demands (while dealing with local production sites, language and culture), to produce plastic car parts wherever OEMs established business, even in remote locations, and to match the customer requirements in terms of quality and schedule
- Lack of Real-Time Data Collection – Management and staff wanted to learn more quickly what was happening to be more efficient and achieve higher customer satisfaction.
- Managing with Just-In-Time (JIT) – Arkal looked for ways to ensure flexible delivery of performance and quality.
- Communication & Reporting Problems – Manual reporting was a lengthy process, prone to human error.
“Management and staff have access to production data to know what’s happening on-the-spot for top-down and bottom-up communications – from anywhere in the world. Matics gives a clear, graphical way to understand production flow and real-time KPIs.”
Yehuda Bakal, Global Information Systems Manager
The Solution
At various points in time, the Matics plug & play solution transformed multiple Arkal sites across Spain, USA, Germany, Canada, and China. With a train-the-trainer approach, Matics self-deployment occurred internationally, giving instant success management tools to each factory.
Team members in every country were able to easily deploy the data analytics shop floor platform via its multi-language interface. The setup of each site was a fast process that only took a few hours. Matics quickly became central to every plant manager and team’s morning meetings.
Upon adopting the solution, Arkal users gained instant visibility and understanding of their data to drive business value. Then in the next stages, a deeper change took place as Arkal teams developed a continuous learning culture that drove more extensive product adoption by local staff.
Arkal experienced two levels of achievements based on these insights:
- Overall, the business accomplished team collaboration across global factories. Each local factory site gained a greater awareness of its performance, improved internal communications, and cultivated a tradition of continuous improvement.
- The headquarters gained a better tool for consistent management of their remote operations and strategic focus looking ahead in the next few years.
“In general, this system has a huge added value with a clear ROI. Matics does more than provide ROI on its software. Matics is willing to partner on meeting our customer requirements anywhere in the world.”
Yehuda Bakal, Global Information Systems Manager
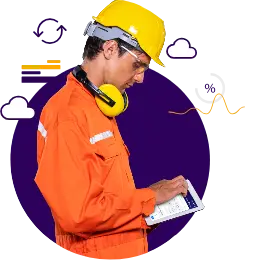
Changing the way people work in factories
Request a DemoThe bottom line?
Capitalizing on new data uncovered by Matics, Arkal was able
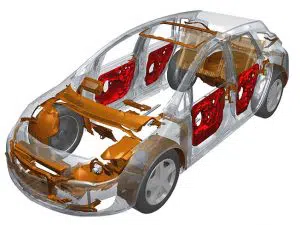
As a result of Matics implementation, a new culture emerged that was collaborative, transparent, and empowered everyone on the production floors. As the pervasiveness of data grew, a cultural shift occurred. People realized their impact. Due to the real-time visual representations of their work, they felt the significance of their daily contributions – an intangible benefit.
Today, Matics also guides Arkal’s capacity planning in existing plants, and in the future, it will support planning when building new sites, drawing on estimates from historic and real-time activities. In addition, Arkal is considering additional modules to monitor, analyze, and further enhance its quality assurance and equipment maintenance.